Quality Control in African Casting: Why It Matters for Success
In manufacturing, especially casting, quality control (QC) is the backbone of success. Quality control is key. It ensures that products, such as African crafts and industrial designs, meet high performance and reliability standards. This is no less true in African casting, an industry that has experienced a boom in recent years. With this growth, challenges arise. Strong quality control measures are key for ongoing success.
This article explores why quality control matters in Africa’s casting industry. It discusses challenges businesses encounter and shares strategies to overcome them. We will also look at real-world examples of companies that used quality control. This led to their success and growth.
Did you know that poor casting quality can harm businesses? It can cause financial losses and damage their reputation. In Africa, the casting industry is booming. Strong quality control can set you apart in a competitive market. Ready to dive in? This article will explore four areas of African casting. They are: 1. The importance of quality control. 2. The challenges faced. 3. Effective strategies. 4. Real-world examples. These can help improve your work or business.
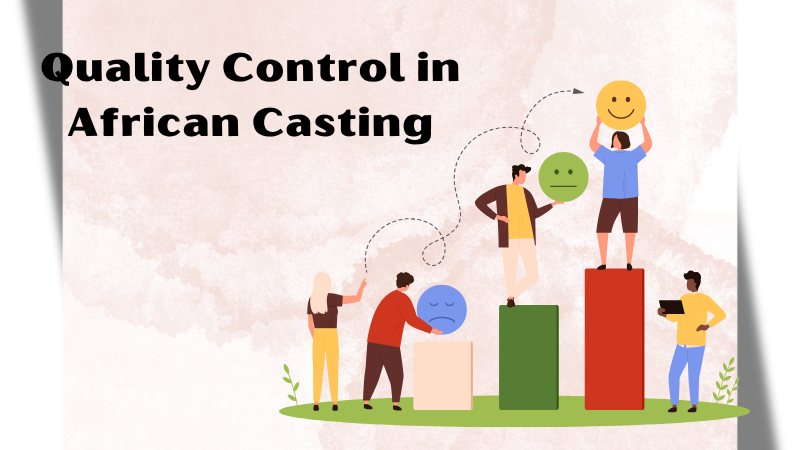
What is Quality Control in Casting?
Quality control (QC) in casting is a process.
Quality control in casting checks if cast products meet standards and are free of defects. The process has several stages. It starts with choosing raw materials and ends with final inspection. The goal is to avoid flaws that could impact the product’s performance or look. Quality control in casting covers several key aspects. It starts with keeping a uniform temperature during melting. Then, it involves using the right materials and inspecting the cast molds. Finally, there’s a thorough inspection of the finished product.
Why is Quality Control Crucial in Casting?
Quality control isn’t just an option; it’s a necessity in casting. Here’s why it’s so crucial:
1. Prevention of Defects
A strong quality control process spots defects early. This way, issues get fixed before the product hits the market. Defects vary from cosmetic problems to serious structural failures. Both can hurt a company’s reputation and lead to costly rework or product recalls.
2. Cost Savings
By reducing defects and rework, quality control saves both time and money. Investing in quality control systems costs money at first. However, over time, the savings from fewer defects, reworks, and returns are worth it.
3. Customer Loyalty and Reputation
A company that makes high-quality products builds a strong reputation. This reliability can lead to customer loyalty and more repeat business. On the other hand, poor quality can damage a company’s reputation and drive customers to competitors.
4. Compliance with Standards
Many industries, like automotive, aerospace, and construction, have strict safety and performance standards. Good quality control helps casting companies meet standards. This way, they can avoid legal problems and failed inspections.
Challenges in Quality Control in African Casting
Quality control is important, but casting companies in Africa face challenges. These challenges can make it hard to implement effective QC processes. Let’s look at some of the primary obstacles:
1. Limited Resources
Many casting companies, especially small and medium ones, often lack money and staff. They might lack the funds to invest in better quality control systems. They may not even have the equipment needed to monitor and enforce quality standards. A survey from the African Casting Association found that over 60% of African casting companies see limited resources as a major challenge for quality control.
2. Skill Gaps
There is a shortage of skilled workers in the African casting industry. Some employees might not have formal training in modern casting techniques or quality assurance practices. This skills gap can lead to inconsistencies in the quality of the final products.
3. Infrastructure Issues
Inconsistent electricity and poor transportation can seriously hinder manufacturing in Africa, including casting. Irregular power supply can impact the furnace temperature or melt process. This can cause defects in casting. Poor transportation can slow down the delivery of raw materials or finished goods. This can disrupt the workflow.
Did you know? A survey by the African Casting Association found that over 60% of casting companies said limited resources are a major challenge in effective QC.
How Can African Casting Companies Improve Quality Control?
Improving quality control in African casting is achievable with strategic approaches. Here are some effective strategies:
1. Invest in Training
Training workers in the latest casting and quality control techniques can improve quality. Consider implementing regular workshops and skill development programmes.
2. Utilise Technology
Embracing technology can streamline quality control processes. Here are a few tools to consider:
- Automated Inspection Systems: These can detect defects in real time, reducing manual errors.
- Data Analytics: Using data to track quality metrics can reveal areas for improvement.
3. Develop Standard Operating Procedures (SOPs)
Clear SOPs for every stage of the casting process ensure quality and consistency. Make sure to document procedures and train your staff accordingly.
4. Foster a Quality Culture
Encourage all employees to take ownership of quality. We can do this with incentive programmes. They should reward quality work and lower defects.
Want to know a secret? Companies that prioritize a quality culture have happier employees and lower turnover. Happy employees tend to produce better quality work!
Real-World Examples of Successful Quality Control in African Casting
Let’s look at a few companies that have used quality control in their casting processes.
Example 1: CastAfrica Ltd.
CastAfrica, based in Nigeria, struggled with a lack of skilled workers. They invested in a training programme. It cut defects by 30% in two years. Their focus on quality has won contracts with major car makers. It proves that investing in people pays off.
Example 2: South African Foundry
This foundry adopted automated inspection systems. They now catch defects before they reach the customer. They saw a 20% boost in customer satisfaction. This led to repeat business and referrals.
FAQs
Quality control in casting ensures all standards are met. It involves inspecting materials, monitoring processes, and testing the final product.
Companies can partner with schools to train staff. They can also seek funding from international organisations.
Training teaches employees to spot and fix quality issues quickly.
Technology enhances precision, reduces human error, and facilitates data-driven decisions for continuous improvement.
Companies can track defect rates, customer satisfaction, and return rates. These metrics gauge the effectiveness of their quality control.
Quick Reference Guide
- Key Strategies: Invest in training, use technology, develop SOPs, and foster a quality culture.
- Challenges: Limited resources, skill gaps, infrastructure issues.
- Success Stories: CastAfrica and a South African foundry.
- Metrics for Success: Track defect rates, customer satisfaction, and repeat business.
Conclusion: The Path Forward
Conclusion: The Path Forward
In conclusion, quality control in African casting isn’t just a rule. It’s a must for business success. Companies that focus on quality control will stand out. This includes training, using the right technology, and following standard procedures. In a competitive market, these steps make a big difference. African casting companies can boost product quality and customer satisfaction. They can do this by overcoming challenges like resource limits and skill gaps. This, in turn, will help drive business growth.
If you work in casting or want to start, focus on quality control. Investing in it today will pay off tomorrow. You’ll see better products, happier customers, and a stronger bottom line.
Let us know in the comments what quality control measures have worked for your business. What challenges have you overcome, and how has it helped you succeed?